TECNOLOGÍA DE METALIZACIÓN EN PLÁSTICOS
Ciclo Convencional x Metalización Directa x Sistema Iónico
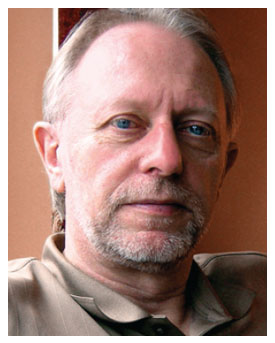
"Los sistemas coloidales convencionales continúan siendo los más confiables, versátiles y con menor costo. La metalización directa continúa siendo un nicho de mercado. Y los más recientes sistemas iónicos ofrecen flexibilidad."
ABSTRACT
A summary of the strengths and weaknesses of plastic pretreatment systems. Why is conventional pretreatment so strong and widely adopted and yet new systems like direct metallization are slow to take hold. The arguments are put forward that might help to explain why this is and point to future developments that may offer routes for more tangible advances.
Un resumen de las ventajas y desventajas de los sistemas de pretratamiento para plásticos.
¿Por qué el pretratamiento convencional robusto es ampliamente adoptado y, además, los sistemas nuevos, como la metalización directa, lentamente intentan entrar en el mercado?
Los argumentos son citados a continuación y pueden ayudar a entender el porqué y señalar desarrollos futuros que puedan ofrecer caminos más tangibles y avanzados.
¿POR QUÉ LA INDUSTRIA AUTOMOTRIZ ES TAN IMPORTANTE PARA LA METALIZACIÓN EN PLÁSTICOS?
Todos los fabricantes de vehículos utilizan la metalización en plásticos de automóviles de paseo, consumiendo aproximadamente 50% de toda la producción de metalización en plásticos.
Los fabricantes de vehículos poseen los más altos estándares de calidad y por este motivo marcan la dirección de este mercado.
MERCADO GLOBAL DE METALIZACIÓN EN PLÁSTICOS – ABS
El mercado de inyecciones en plásticos consume anualmente aproximadamente 10 millones de toneladas en ABS, de las cuales un 25 - 30% tienen como destino el mercado automotriz. Algunos dados del mercado de metalización en plásticos:
• Aproximadamente 200 aplicadores en el mundo;
• 70 millones de m2 (70 km2) por año procesados;
• 9,000 toneladas de cobre (Media de 15 um);
• 9,000 toneladas de níquel (Media de 15 um);
• 1,000 toneladas de cromo (Media de 0,2 um);
TIPOS DE PRETRATAMIENTOS PARA METALIZACIÓN EN PLÁSTICOS
Existen tres tipos de pretratamientos para metalización en plásticos en uso comercial: convencional, metalización directa y ciclo corto (Iónico). Los procesos de electrodeposición son comunes a los tres tipos. El sistema convencional está en producción hace ya más de 30 años y es utilizado por la mayoría de los fabricantes actuales de piezas.
El sistema convencional ofrece los siguientes beneficios ya conocidos:
• Trabaja con múltiples substratos: ABS, PP y aleaciones ABS/PC;
• Depósito químico de alta adhesión (níquel químico o cobre);
• Elevado conocimiento técnico;
• Tasas de rechazo bajas;
• Sin agentes de complejidad fuertes (opcional);
• Aditivos exentos de PFOS.
La metalización directa exhibe las siguientes ventajas:
• Ciclo de proceso más corto (tiempo y tanques necesarios);
• Menor costo;
• Sin agentes de complejidad;
• Sin depósitos químicos;
• Sin depósitos strike;
• Rechazos reducidos;
• Puede ser usada para ABS y ABS/PC;
• Sin acumulación de depósito en los ganchos.
El sistema iónico tiene como característica principal activadores iónicos con bajas concentraciones de paladio meta:
• Ciclo corto (5 etapas);
• Baja concentración de paladio (20 ppm);
• Excelente doble capacidad para moldeado;
• Alta tolerancia a la contaminación;
• Óptimo desempeño en múltiples substratos y aleaciones de PC;
• Menor costo;
• Gestión de proceso simplificada.
Metalización directa: beneficios anunciados
A continuación un análisis detallado de cada beneficio anunciado para la metalización directa y una tentativa de entender porqué la adopción de este sistema en un período de 20 años viene siendo tan lenta.
a- Primera ventaja anunciada: Número menor de pasos de procesos y menor tiempo de proceso
La "metalización directa" posee cuatro etapas principales de procesos, mientras el sistema convencional posee cinco, por tanto la metalización directa usa un proceso menos. No obstante, los aplicadores no pueden usar este argumento como una ventaja real, ni incluso en la fabricación de la línea con una etapa menos. Una línea montada para pretratamiento convencional es más flexible y de fácil adaptación.
• 30% de reducción en el tiempo de ciclo:
Tiempo de la línea de metalización directa: 19 minutos; tiempo del ciclo convencional: 23 minutos
La diferencia entre los tiempos de ciclo es de 4 minutos (17%), aunque sin un significativo aumento de la capacidad de electrodeposición, la ventaja de reducción de tiempo de línea no puede ser aprovechada.
La efectiva economía de tiempo, 4 minutos, representa solamente 2% del total del ciclo completo de la metalización en plásticos.
b- Segunda ventaja anunciada: Sin baños químicos
La metalización directa anuncia no tener baños químicos (cobre y níquel), aunque en el lugar de estos procesos es usado un baño de cobre/estaño. Al momento del cambio entre estaño y cobre existe una aceleración, lo que no se da en los otros baños. Sin embargo, esta ventaja es descartada por el costo operacional mucho mayor. Aproximadamente 30% del total del costo de la línea de pretratamiento está relacionado con la etapa química y el consumo primario es por arrastre.
Baños convencionales de níquel químico consisten en 13 - 15% de aditivos propietarios, mientras los baños de inmersión de la metalización directa poseen 40% de aditivos propietarios. En precios equivalentes, los costos de arrastre son:
• "Convencional" a USD1.0/litro = USD0.13
• "Metalización directa" a USD1.0/litro = USD0.40
c- Tercera ventaja anunciada: Sin baño "strike"
La metalización directa anuncia que no hay baños "strike", mientras la etapa del cobre ácido debe tener un pico de corriente de 3 a 5 minutos para la propagación del depósito controlado, aunque usa la etapa del baño de cobre ácido como un baño, ocupando la capacidad valiosa de este baño.
"La línea convencional" puede ser usada sin un baño "strike" y más de 50 % de los aplicadores convencionales no usan un baño "strike" dedicado.
d- Cuarta ventaja anunciada: Fácil integración en la planta existente
Los procesos de metalización directa usan un tanque menos y, por tanto, encajan en las líneas convencionales existentes. No obstante, una línea de proceso construida para la metalización directa no puede operar un proceso convencional sin una gran inversión. Para nuevos equipamientos, el costo de la capacidad convencional versus el de la metalización directa es de 7 - 10% del total del valor de la planta, pero aumenta la flexibilidad de proceso y de la planta si estas inversiones son realizadas en el proyecto inicial y la fase de construcción.
e- Quinta ventaja anunciada: Alta confianza en la producción
La metalización directa no está presente en ningún gran aplicador que produzca piezas para la industria automotriz en Europa y en los Estados Unidos. No es posible arribar a conclusiones en producciones de aplicadores pequeños, pero dado la falta de este proceso en el mercado es muy improbable que cualquier ventaja relacionada confiablemente con producción sea autosustentable.
f- Sexta ventaja anunciada: Menor índice de rechazo
Las causas más comunes de rechazos en metalización en plásticos son aspereza y pitting, típicamente causados por partículas que son generadas por la quema de piezas localizadas en las puntas de los ganchos. El pretratamiento convencional con níquel químico tiene una típica resistencia de 20-50 ohms/cm. El depósito de inmersión de la metalización directa posee una alta resistencia eléctrica (125-200 ohms/cm) y necesita más puntos de contacto en ganchos por artículo. En particular, colocar piezas mayores en ganchos requiere más puntos de contacto debido a la baja propagación de cobre electrodepositado. La metalización directa aplica una capa de cobre muy débil, seguida del cambio Cu-Sn, que debe ser depositado lentamente con cobre ácido para evitar el contacto en la punta de los ganchos. Son necesarios muchos puntos de contacto para garantizar una buena propagación del depósito.
Muchas puntas de ganchos normalmente representarán un alto riesgo de rugosidad y, de esta forma, es difícil saber cómo el bajo índice de rechazos será alcanzado.
g- Séptima ventaja anunciada: Sin limitaciones de Substratos
El ABS/PC está alcanzando el 50% del mercado de substratos. La metalización necesita procesos extra más caros para procesar T45 y aleaciones T65 ABS/PC. La metalización directa usualmente precisa 10 - 20 ppm de paladio en la activación crómica para la obtención de un proceso confiable en aleaciones de ABS/PC.
La metalización directa también necesita promotores de paladio para procesar ABS/PC. El pretratamiento convencional puede procesar la mayoría del ABS/PC sin procesos químicos extra o modificaciones especiales.
h- Octava ventaja anunciada: Bajo costo
Posiblemente la única diferencia más importante entre la metalización directa y el tratamiento convencional es la concentración del activador. Típicamente 50% del costo del pretratamiento se refiere a la etapa del activador de paladio.
El costo actual de la LME para paladio es de USD 21,00/g, siendo que el pretratamiento convencional usa 40 ppm de paladio y la metalización directa utiliza hasta 240 ppm de paladio. Abajo, una comparación de los costos de la materia prima paladio con las variaciones de las concentraciones del metal:
• Convencional a 40ppm = USD0.84/Lt
• "Metalización Directa" A a 120ppm = USD2.50/Lt
• "Metalización Directa" B a 200ppm = USD4.20/Lt
Es imposible que la metalización directa tenga un costo operacional menor, cuando se lo compara con el pretratamiento convencional. Los desarrollos para los procesos de metalización directa se han centrado en la disminución de la concentración de paladio, aunque esto también compromete los principios químicos básicos por detrás del proceso y reduce de forma significativa su confiabilidad. Esta es posiblemente la más importante razón por la cual la metalización directa falló en intentar ganar credibilidad en el mercado.
i- Novena ventaja anunciada: Menos depósitos en ganchos
Los depósitos en ganchos son bien conocidos por resultar de altas concentraciones de paladio y actividad, y la metalización directa tiene la mayor concentración de este componente en comparación con cualquier sistema conocido. El sistema de metalización directa es conocido por causar una acumulación de depósito en ganchos, lo que resulta en mayores índices de rechazo y un alto costo.
j- Décima ventaja anunciada: Fácil tratamiento de efluentes
Excluyendo el cromo, la complejidad del tratamiento de efluentes y costos son dedicados a las etapas de los lavados provenientes del activador, acelerador (Sn/ Pd) y níquel químico (Ni). La metalización directa usa 4 veces más concentración de estaño en la etapa del activador y, por tanto, precisa más tratamiento de efluentes. La metalización directa también utiliza cobre por inmersión con 40% en volumen de aditivos que deben ser tratados. En el pretratamiento convencional es posible usar níquel químico exento de amoniaco, el cual es mucho más fácil de ser tratado. Presentando estas diferencias es difícil entender la justificación para afirmar que se da un fácil tratamiento de efluentes.
RESUMEN
Beneficios de la metalización directa que fueron considerados:
• Número menor de etapas de procesos:
No significativo
• Economía en el tiempo del ciclo:
¿2% de reducción es significativo?
• Costo:
Mucho mayor (3 veces)
• No tiene baño "strike"; Se utiliza cobre ácido
• Substratos;
Mayor costo para el ABS/PC
• Índices de rechazo; Mayor riesgo
• Enganche; más complejo
• Deposición en los ganchos; Mayor riesgo
• Tratamiento de efluentes; más complejo
METALIZACIÓN DIRECTA EN EL MERCADO GLOBAL
Con la pequeña adopción por tan pocos aplicadores del proceso de metalización directa y con ningún beneficio realmente técnico, es difícil advertir una justificación técnica para el proceso. El desarrollo del proceso de metalización directa fue centrado en la reducción de la concentración de paladio, lo que demuestra una debilidad en relación al costo en la introducción de este pretratamiento. A pesar de afirmarse que el proceso es usado en Japón, el mayor costo no puede ser fácilmente justificado en mercados más competitivos. A pesar de haber sido introducido hace más de 20 años, aún permanece como nicho y relativamente sin utilización. La evidencia para la falta de éxito se basa en los análisis anteriores, aparentando que estas debilidades fundamentales en el proceso no pueden ser superadas.
Una alternativa real: ciclo corto utilizando paladio coloidal - infinity™
El progreso en la ciencia del activador coloidal ha también conducido a desarrollos en activadores iónicos, para ayudar a reducir la confianza en el paladio y ofrecer un ciclo corto con un costo genuinamente bajo. Este proceso también se encuadra perfectamente en el aumento de la demanda en procesar plásticos de moldes dobles.
Beneficios
• Menor concentración de paladio (15 a 20 ppm);
• Menor costo en comparación con la metalización directa;
• Catalizador iónico altamente estable;
• Ciclo de 4 etapas;
• Flexibilidad para depositar aleaciones comunes de ABS/ PC;
• Ideal para moldes dobles;
• Necesidades tradicionales de enganches.
LA CIENCIA DE LOS COLOlDES
El paladio coloidal es una mixtura de partículas de paladio envueltas en una circunferencia de cloruro de estaño.
Su estructura es un coloide semiestable que posee una carga electronegativa fuerte que es opuesta al ABS (+). Como en la teoría de la atracción magnética, donde cargas opuestas se atraen, este mecanismo es igual, alentando el paladio a adherirse a la superficie de plástico activada y mojada. Para estabilizar los núcleos de paladio, ellos son cercados por una capa de estaño. Luego de la adsorción a la superficie del plástico, el Sn externo puede entonces ser removido para exponer el paladio, el cual se torna catalizador para el níquel químico y el cobre.
PALADIO IÓNICO
El paladio iónico es esencialmente paladio en solución, donde el rayo iónico (de 2+ iones) es de 73 picómetros. Esto produce una solución de baja concentración, altamente estable, que no es contaminada por cromo, níquel o cobre y es una superficie ideal de activación para la deposición química. No existe necesidad de una etapa de neutralización, dado que el catalizador iónico no es afectado por los bajos niveles de cromo que restan en la superficie tras la activación y el enjuague
Ciclo iónico típico |
|
Activación |
8 -12 min a 68°C |
Enjuague x 2 |
|
Activador |
5 min a 28°C |
Enjuague x 2 |
|
Reductor |
4 min a 40°C |
Enjuague x1 |
|
Níquel químico |
7 min a 30°C |
Realizar la conversión para el paladio iónico no requiere ninguna alteración en los equipamientos, tanques, ganchos, calentamiento, etc. Su instalación en antiguas líneas convencionales y de metalización directa es simple y opera significativamente a menores costos que los procesos de metalización directa.
Los sistemas iónicos ofrecen un desempeño de proceso y calidad de acabamiento equivalente a los procesos convencionales y, debido a la naturaleza altamente selectiva del catalizador, son ideales para aplicaciones de moldes dobles.
EN RESUMEN
La demanda de metalización en plásticos continúa creciendo en mercados globales impulsados principalmente por el consumo del sector automotriz.
Los sistemas coloidales convencionales continúan siendo los más confiables, versátiles y con menor costo en el mercado global. 20 años después de su introducción, la metalización directa continúa siendo un nicho de mercado. Los más recientes sistemas iónicos ofrecen flexibilidad y un potencial genuino de reducción de costo para el futuro
La demanda del sector automotriz continúa guiando las innovaciones en metalización en plásticos. Lo que esperamos ver en los próximos años son activadores coloidales de alto desempeño, aumento del uso de sistemas iónicos guiados por reducción de costo y, talvez, eventuales alternativas a los activadores a base de paladio.
<< Boletin Acabados Superficiales - Edición de noviembre 2012
Terry Clarke
Director global, Productos Decorativos de MacDermid Inc.
Traducción:
Flaviana V. Zanini Agnelli
Directora técnica y operacional de Anion MacDermid |