METALIZACIÓN DIRECTA DE PLÁSTICOS
ABS y ABS-PC
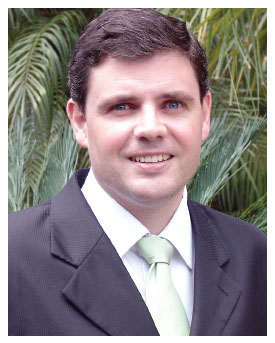
"Es posible afirmar que con los nuevos procesos de metalización directa podemos alcanzar una reducción de costos en el paladio perdido por arrastre. Para otras reducciones de costos, además de la optimización del proceso químico, es necesario acompañar atentamente y hasta optimizar todos los parámetros involucrados en la adsorción."
ABSTRACT
For many years direct plating processes are increasingly being used in different industries plating ABS and ABS-PC plastics. Due to a lower number of process steps, advantages were observed in the process. The key of the direct metallization is the replacement of the Sn-Pb colloid by the copper, without the application of the conventional Electroless Nickel. Due to the price increase of the palladium, new generation of the process was developed in order to reduce significantly the amount of the palladium in the activator baths. The cost save was observed mainly because of the less Pd lost in the drag-out.
Desde hace aproximadamente 17 años los procesos de metalización directa vienen siendo usados cada vez más en diferentes segmentos, como en la industria de metales sanitarios y automotriz, y en la metalización de piezas plásticas en ABS y ABS-PC. Además de que la secuencia del proceso es más corta y de mejor control, en comparación con los procesos de níquel químico, existe la posibilidad de producción con relativa reducción en las tasas de rechazo. Estas son las razones que tornan este tipo de aplicación particularmente interesante. Debido al menor número de etapas en el proceso y de los diferentes productos químicos utilizados, existe una ligera ventaja en relación al método convencional de metalización de plásticos también en términos de los residuos a ser tratados en la estación de tratamiento de efluentes.
La Figura 1 muestra la secuencia del proceso de metalización directa empleando el proceso Neolink®.
(Metalización Directa - Desengrase (opcional) > Acondicionador > Cr (Vl)-Reducción > Preactivación > Activación > Cu-Link > Línea Electrolítica)
EL MECANISMO DE LA METALIZACIÓN DIRECTA
La clave para el éxito de esta tecnología reside en la adsorción del coloide de estaño-paladio en la superficie del plástico, inmediatamente después de su acondicionamiento en solución sulfocrómica (baño de ácido crómico/ácido sulfúrico). La figura 2 muestra el diseño de un coloide de acuerdo con la literatura [1].
Metalización de Plásticos
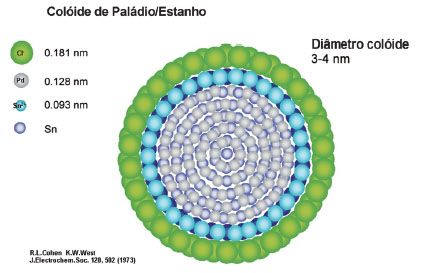
La capa externa está constituida por una capa protectora de SnCl3-, que carga la superficie del coloide y, de esta forma, impide la aglomeración de las partículas. El interior del coloide está constituido por estaño y paladio en la forma metálica [2]. Presumiblemente, los coloides adsorbidos sobre la superficie del plástico construyen una capa conductora a través de varios mecanismos con una solución alcalina correspondiente a la base de cobre (como el Futuron Ultra Cu-link, Neolink®). Luego de retirar el coloide protector en la solución alcalina a base de cobre, parece posible el cambio directo del estaño metálico en el interior del coloide con el cobre [3]. No obstante, es más probable que la estabilidad relativamente baja de los complejos de Cu2+ en las soluciones alcalinas de proceso sea responsable por la formación de la capa conductora. Como resultado, el óxido de Cu-(I) puede ser formado por la reducción de Cu2+ por el Sn2+. El óxido de Cu-(I) puede, en adición a sus propiedades semiconductoras, tornarse desproporcionado dentro de un baño de cobre.
En general, todas las reacciones parciales mencionadas pueden contribuir para la formación de una capa reticulada, fina y conductora. Esto se tornó evidente en diversos estudios en que Cu0 y Cu+, así como Cu2+ fueron rastreados a lo largo de la superficie [2]. La necesidad de esta capa para la subsiguiente deposición de cobre puede ser explicada por la figura 3 [4]. La formación de la capa de cobre es construida a partir del contacto en el cátodo en la dirección lateral. En la literatura, diferentes informaciones sobre este tipo de crecimiento lateral de la capa de cobre en el baño de cobre ácido pueden ser encontradas [4, 5, 6].
Cobre Respectivo
Óxido de Cobre (I)
Coloide de Paladio
Estaño
DESARROLLO DE LA METALIZACIÓN DIRECTA
Los primeros años posteriores a la introducción de esta tecnología se vieron influenciados por los precios relativamente bajos del paladio. A mediados de la década pasada, a más tardar, hubo un notable aumento de los precios del pala¬dio, lo que hizo que esta aplicación se torne menos atractiva. Una parte del desarrollo de la metalización directa durante los últimos 10 años fue, por tanto, dedicada a la optimización en la utilización del paladio. Esto puede ser ilus¬trado a través del proceso Futuron®. Este proceso fue introducido en el mercado en 1995 y muy pronto alcanzó penetración en el mercado global. La concentra¬ción de paladio en los baños de activador era de cerca de 250 mg/L. A través de los diez años siguientes, la canti¬dad de paladio necesaria para la activación fue reducida a 190 - 200 mg/L, debido a la optimización de las secuencias del proceso en las líneas de los cromadores. Debido a la introducción de una nueva generación del proceso - proceso Futuron® Ultra - otra reducción de paladio en los baños de activador fue alcanzada; en promedio 120 mg/L de pa¬ladio eran necesarios para la metalización de plásticos ABS y ABS-PC con este proceso. Esto correspondió a una reducción de 1/3 de paladio, a través de la mejoría de los activadores de paladio y de la solución alcalina de cobre, el así llamado Futuron Ultra Cu-Link. Ninguna limitación en términos de calidad o funcionalidad fue observada.
Las razones para la promoción de este tipo de desarrollo pueden ser ilustradas con los cálculos abajo:
En un baño de activador que contiene 250 mg/paladio, a 0,2 L/m2 de arrastre, 500 m2 de área son tratados por día. Esto genera una pérdida de 25 g/500 m2 de paladio siendo arrastrados sin activar la superficie. El mismo cálculo para una concentración de activador de 120 mg/L de paladio genera una pérdida de 12g/500 m2 de paladio.
El desarrollo de los procesos de metalización directa además se concentra en la reducción del consumo de paladio. Por este medio, los procesos más recientes, tales como el proceso Neolink®, pueden ayudar a reducir la cantidad de paladio necesaria. No obstante, otras variables del proceso deben ser enfocadas.
Además del arrastre arriba mencionado, la adsorción necesaria en la metalización directa contribuye significativamente para el consumo. La adsorción de las partículas de paladio sobre las superficies de plástico, sin embargo, depende de muchos parámetros diferentes, tales como el tipo de plástico, los parámetros durante la inyección de plástico, los parámetros de acondicionamiento y los parámetros aplicados en el activador de paladio.
El tipo de plástico y, respectivamente, sus parámetros durante la inyección representado por diferentes piezas (geometrías)
Para conocer el consumo total del paladio adsorbido, diferentes plásticos ABS y sus parámetros de inyección deben ser considerados.
Figura 4: Muestra la cantidad de paladio [mg/m2] adsorbida en la superficie de diferentes polímeros de ABS, bajo las mismas condiciones de proceso, respectivamente, en tres
diferentes formas de piezas
Dependiendo del tipo del polímero y de las condiciones de la inyección, diferencias de hasta 100% surgen en la adsorción de paladio. Con estos hechos, el cálculo de consumo arriba enumerado puede ser extendido:
Consumo de paladio por adsorción: 100 mg/m2
Tenor de paladio en el baño activador 55 mg/L
Producción diaria: 500 m2
Arrastre: 0,2 L/m2
Esto equivale a un consumo total de:
Pd/500m2: 55,5 g
El equivalente de un plástico a ser metalizado con 50 mg/m2 de adsorción de paladio:
Pd/500 m2: 30,5 g
Alterando un parámetro del activador; por ejemplo, la concentración de paladio
Cuando alteramos un parámetro en el baño de activador, por ejemplo, con reducción de la concentración de paladio, menos partículas del activador son susceptibles de ser adsorbidas en la superficie.
Un ejemplo es ilustrado en la Figura 5. Las diferentes concentraciones de paladio en el baño activador resultan en diferencias notables en la relación de adsorción del paladio, manteniéndose los demás parámetros inalterados.
Figura 5: Dependencia de la concentración de paladio Pd [mg/m2] en 3 diferentes piezas plásticas, inyectadas en el mismo polímero, pero con diferentes concentraciones de paladio (55 mg/L y 110 mg/L)
En ambos casos, la superficie puede ser metalizada en el baño de cobre ácido sin dificultades. Esto significa que la cantidad necesaria de paladio adsorbida es conseguida en el activador con 55 mg/L, y el excedente, adsorbido en un baño de activador de 110 mg/L, es consumido sin ningún beneficio directo. La concentración es apenas un parámetro dentro del activador de paladio que tiene impacto en la cantidad de paladio adsorbida en la superficie del plástico. Parámetros adicionales, relevantes para la optimización de la adsorción de paladio, son la temperatura, tiempo de exposición y concentración de estaño.
RESUMEN
En resumen, se puede decir que con los nuevos procesos de metalización directa podemos alcanzar una reducción de costos en el paladio perdido por arrastre. Para reducciones adicionales de costos, además de la optimización del proceso químico, es necesario acompañar atentamente y, eventualmente, optimizar todos los parámetros involucrados en la adsorción.
<< Boletin Acabados Superficiales - Edición de noviembre 2012
Dr. Carl Fels
R&D Manager - GMF
Deco/Plating on Plastics
Atotech Deutschland GmbH
Traducción y complementación del artículo:
Anderson Bos
Gerente de Producto - Deco/POP de Atotech de Brasil |