¿SUS TORNILLOS REVESTIDOS SON CANDIDATOS A FALLAS CATASTRÓFICAS?
"Aquí son enfocados los sistemas de revestimiento de fluoropolímeros, desarrollados hace 40 años como lubrificantes de capa fina, para superar el problema específico de alcanzar valores de torque uniformes alrededor de una rosca."
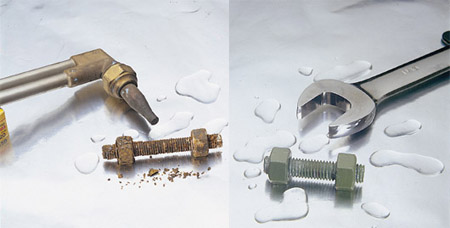
Un tornillo mal revestido x un tornillo debidamente revestido. ¿Cuál fallaría primero? ¿Cuál sería más fácilmente removido para mantenimiento a 20.000 metros debajo del agua?
Esa no es una cuestión sin importancia. Las plataformas de extracción de petróleo en altamar (y otras estructuras similares expuestas a ambientes altamente corrosivos) son compuestas de millares de piezas diferentes, siendo que algunas de las menores y aparentemente más insignificantes son los tornillos revestidos, que mantienen la estructura. Si ellos fallasen repentinamente, los resultados pueden, de hecho, ser catastróficos.
Es ahí que los sistemas de revestimiento de fluoropolímeros entran.
Estos revestimientos fueron desarrollados hace 40 años como lubrificantes de capa fina, para superar el problema específico de alcanzar valores de torque uniformes alrededor de una rosca. Los sistemas entonces vigentes, de “fosfato y óleo” o “liga de grafito y bisulfato e molibdeno”, simplemente no alcanzaban fricción uniforme en cada tornillo.
Nota: El hecho de que estos sistemas de revestimiento reducen la constitución del torque significa que es esencial recalcular la cantidad reducida de torque necesaria para alcanzar la carga ideal de fijación. Al ser negligentes con eso, podemos exceder la resistencia de presión del tornillo, lo que podrá causar "destrabamiento” o la falla catastrófica del tornillo.
¿Cuántos millares de tornillos revestidos están manteniendo esta plataforma? ¿Todos ellos fueron revestidos adecuadamente?
¿Y la corrosión?
Ya que la corrosión y el daño resultante de tales tornillos eran un problema serio, los ingenieros que describieron tales revestimientos querían saber si los nuevos productos de fluoropolímeros podrían ser adaptados, para ayudar, también, en la prevención de la corrosión.
La respuesta fue si, a través de la combinación del revestimiento de fluoropolímero con una variedad de pre tratamientos, para proveer lo mejor en protección contra la corrosión.
Esos sistemas de revestimientos fueron lanzados con instrucciones específicas en relación a los pre tratamientos, primers, métodos de aplicación, etc., para garantizar calidad máxima en esa área. Como era esperado, a veces debido a la falta de experiencia, se saltan muchas etapas y surgen los problemas.
Los problemas
En algunos casos, revestidores de mala reputación simplemente aplicaban pintura a los tornillos. La preparación de la superficie a veces era mal hecha o ignorada. Los pre tratamientos y primers de extrema importancia no eran usados. El espesor de la capa no era controlada. Las temperaturas de cura estaban, en la mayoría de las veces, equivocadas. Las tuercas no eran mayores para compensar el espesor del revestimiento. El torque de constitución reducido no era calculado, resultando en sobre compresión. Había falla en la localización de los problemas, cuando ocurrían.
Una combinación de todo eso llevaba, frecuentemente, a fallas de gran valor en el área, confusión del usuario final y una deterioración de la reputación de aquellos que aplicaban el revestimiento.
¿Por qué?
Pintura azul. Los revestimientos originales eran pintados de azul para identificación, entonces el azul es hasta hoy el color más común, seguido del verde. Pero el color no indica que el revestimiento tenga tensión de torque ideal, o resistencia a la corrosión. Solo indica que el tornillo es azul (o verde).
¿Cómo mantener la credibilidad?
Por lo menos un fabricante de tales revestimientos decidió lanzar un método que garantizase la calidad de esos tornillos revestidos. (Nota: Fue una empresa global la que emprendió la tarea de descubrir el tal método)
Azul es el color más popular para los tornillos, seguido del verde. Pero solo el color no garantiza un tornillo bien revestido.
El ensayo de niebla salina ( ASTM B-117) es un elemento llave en el proceso de control de calidad de tornillos revestidos.
En 2008, el fabricante ofreció una solución al crear el Programa “Aplicador de Calidad Aprobada” (QAC), que consiste en un número selecto de revestidores que han comprobado su capacidad de proveer tornillos revestidos dentro de una lista de patrones rigorosos establecida por el fabricante. El objetivo es garantizar, constantemente, la alta calidad de los tornillos revestidos.
Un número limitado de aplicadores conocidos del fabricante de revestimientos, que hayan comprobado su aptitud para ofrecer esta calidad, fue seleccionado e invitado a participar.
Todos ellos estaban sujetos a condiciones específicas y tenían patrones específicos. Ejemplo: Cada miembro tenía que tener un equipo de aplicación específico, incluyendo un sistema de pre tratamiento. Cada una de esas empresas tuvo que enviar a alguien para uno de los laboratorios del fabricante de revestimientos, para un entrenamiento formal de la aplicación adecuada de sus revestimientos. Todos tuvieron que enviar muestras revestidas para una variedad de ensayos de calidad, incluyendo apariencia, espesor de capa seca, cura, ensayo de niebla salina (ASTM B-117), etc. Todos estuvieron de acuerdo en someterse a auditorias hechas aleatoriamente por el fabricante.
Cinco pasos para el suceso
Hay cinco pasos principales en la aplicación de tales sistemas de fluoropolímero. Ninguno es complicado, pero cada uno es crucial para el funcionamiento apropiado final del tornillo:
- Preparación del material: eso incluye la mezcla de los materiales de acuerdo con las instrucciones, midiendo y posiblemente ajustando la viscosidad, caso no esté precisamente como debería.
- Preparación de la pieza: ese paso garantiza que la pieza a ser revestida esté limpia y sin contaminantes y que tenga perfil de superficie apropiado para máxima adherencia.
- Pre tratamiento adecuado: La protección máxima contra la corrosión exige un pre tratamiento o primer. Esos tienen tres categorías: en revestimiento de barrera, un revestimiento preventivo o un revestimiento de sacrificio.
- Espesor de la capa: debe estar correcta no solamente para la pieza, pero también en relación al material del revestimiento elegido. Si la capa es muy fina, ocurrirá alteración en la resistencia a la corrosión. Si es muy gruesa, el revestimiento tiende a quedar suave y sujeto a desgaste y las tuercas no entrarán.
- Condiciones de cura: deben ser suficientes para garantizar que todos los facilitadores (solventes o agua) sean retirados y que la resina de ligación haya sido curada (ligada químicamente) adecuadamente. Normalmente, eso significa que la pieza de metal fue calentada en el horno de cura más allá de los 200 ºC, por, como mínimo, 15 minutos. Las especificaciones de la temperatura de cura y del tiempo siempre se refieren al tiempo en que la parte estuvo a la temperatura correcta, no solamente el horno.
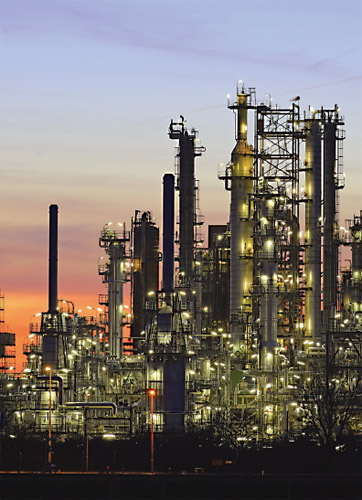
Si estos pasos son seguidos cuidadosamente, los tornillos revestidos tendrán mejor desempeño y los problemas desaparecerán.
Los resultados hasta ahora
El fabricante relata una reacción favorable hasta el momento.
Un porta voz de la empresa dice: “estamos viendo cada vez más usuarios finales que quieren trabajar exclusivamente con los revestidores que hacen parte de Programa de Aplicador de Calidad Aprobada. Muchos de esos son los mismos usuarios finales, que antes reclamaban de la inconstancia de la calidad de los tornillos que recibían. El QAC es bueno para ellos y para la industria”.
El fabricante admite prontamente que ese programa, a pesar de costoso, es de su mayor interés, ya que ayuda a proteger y fortalecer la imagen de calidad de los sistemas de revestimiento proveídos por los aplicadores QAC.
<< Boletin Acabados Superficiales - Edición de marzo 2012
Antônio Ribeiro Cardoso Filho
Gerente de Ventas Industriales de Whitford do Brasil Ltda
|