MÉTODOS NO DESTRUCTIVOS UTILIZADOS PARA MEDIR EL ESPESOR DE CAPA DE REVESTIMIENTOS
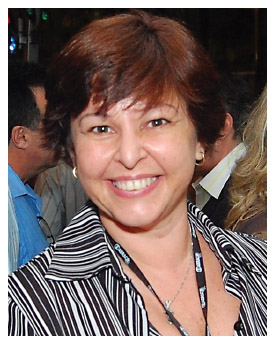
"Las dos especialistas presentan, en esta Orientación Técnica, una breve revisión de los métodos no destructivos de medición de espesor de capa: inducción magnética, corrientes parásitas y fluorescencia de rayos X."
1- INTRODUCCIÓN
La aplicación y calidad de un revestimiento son determinadas por características como resistencia a la corrosión, porosidad, dureza, resistencia al desgaste, apariencia, rugosidad, adhesión, propiedades magnéticas, conductividad eléctrica, tensión interna, espesor de capa, entre otras. En lo que se refiere al espesor de capa, en general, la vida útil de un revestimiento y su calidad aumentan con el aumento de esta característica, tanto que esta medida es usada como control de calidad y test de aceptación de materiales revestidos. Así, se puede decir que el espesor de la capa del revestimiento es un parámetro importante y determinante para fabricantes y usuarios.
Los métodos usualmente empleados en la medida del espesor son clasificados como destructivos y no destructivos. Los primeros inutilizan el material, al paso que estos últimos no requieren la destrucción del mismo.
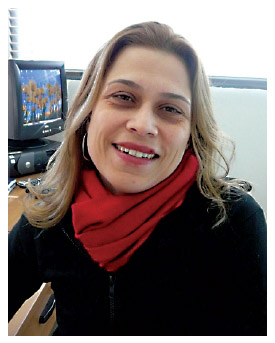
La opción por el método más adecuado depende de la naturaleza del sustrato, necesidad de utilización de la pieza después de la medición, tipo de revestimiento a ser medido, geometría de la pieza, entre otros factores.
En este trabajo será presentada una breve revisión de los métodos no destructivos de medición de espesor de capa, a saber: inducción magnética, corrientes parásitas y fluorescencia de rayos X.
2- MÉTODOS POR INDUCCIÓN MAGNÉTICA
Este método es aplicado a los revestimientos metálicos no ferro magnéticos, como por ejemplo: cinc, cromo, cobre, estaño, níquel, plata, así como para revestimientos orgánicos aplicados sobre sustratos metálicos como acero, hierro y acero inoxidable de la serie 300, obedeciendo la norma ASTM B 499-09(1-2).
El método se basa en el principio de la inducción electromagnética y mide el cambio de flujo magnético (U) en la superficie de una sonda. Esta sonda es compuesta por un magneto permanente o un electroimán, como fuente de campo magnético, el cual generará la señal por inducción magnética al entrar en contacto con el metal base. La variación de la magnitud del flujo sobre la sonda está directamente relacionada con la distancia de la misma con el sustrato (3). De esta forma, el sistema convierte las variaciones del flujo en espesores de capa. Aunque simple, existe la necesidad de calibrar el sistema y esto debe ser realizado con el mismo material del sustrato que recibió el revestimiento, una vez que cada sustrato posee propiedades magnéticas propias (1). La Figura 1 ilustra el principio de la medición por inducción magnética (4).
El sistema está compuesto por un equipo portátil y una sonda específica para cada aplicación. La medición es realizada presionando la superficie de la sonda perpendicularmente a la superficie que será medida. Estos equipos compensan la variación de la presión colocada en la sonda de operador para operador (3).
Las mediciones son afectadas por la geometría de las piezas: hay que tener cuidado de no efectuarlas en los bordes o discontinuidades de la pieza o todavía sobre superficies curvadas.
El rango de medición en que este método puede ser empleado está entre 2 y 1000 µm. La tolerancia típica es de +- 1 % (1,3).
Figura 1 – ilustración del principio de la medición por inducción magnética (4).
3- MÉTODO POR CORRIENTES PARÁSITAS
Ese método es usado para medir el espesor de la capa de revestimientos orgánicos (pintura, barniz) o de revestimiento anódico aplicados en sustratos no ferro magnéticos (aluminio), obedeciendo a la norma ASTM B 244-09 (5). Se trata de un método simple, confiable, preciso y práctico, como el método por inducción magnética.
El funcionamiento se basa en el principio de la inducción electromagnética y, por tanto, es muy similar al método anterior. Pero, la corriente de excitación (I) que circula en la sonda genera un campo electromagnético primario, de alta frecuencia, que induce un flujo de corrientes parásitas. Estas generan un campo magnético secundario que se opone al primario. La resultante entre los campos generados da informaciones sobre las características de la muestra evaluada, entre ellas, el espesor de la capa, que es la distancia entre el sustrato y la sonda (3,6).
La penetración de esas corrientes depende de la conductividad del revestimiento y del sustrato, y es proporcional al espesor de la capa. Si la conductividad eléctrica del revestimiento difiere significativamente del material base (sustrato), la magnitud de las corrientes inducidas variará con el espesor. Estos dos efectos, penetración de la corriente e intensidad, son convertidos en unidades de espesor por el equipo. La Figura 2 ilustra la generación de las corrientes parásitas (4).
En principio, este tipo de medidor puede medir el espesor de cualquier combinación de revestimiento y metal base, desde que exista una diferencia entre sus conductividades.
Este método, también, exige la calibración previa del aparato y son necesarios patrones específicos para cada material a ser medido (1,7). Los manuales de los equipos indican cómo reducir la incerteza de las mediciones (3).
Es importante resaltar que, cuanto menor es la frecuencia utilizada, mayor es la profundidad de las corrientes parásitas, lo que no significa que lo ideal son las bajas frecuencias. Esto porque, cuanto mayor la frecuencia, mayor la sensibilidad del sistema. Se debe entonces elegir la mayor frecuencia posible, desde que sea compatible con los espesores que se pretende medir (6).
Este método tiene menor dependencia de las variaciones de la permeabilidad magnética del metal base. Además de eso, permite medir piezas menores, con superficie rugosa, con curvatura y con geometría compleja. La presencia de cualquier capa intermediaria en la pieza a ser medida deja el equipo no funcional (1,7).
El rango de medición es limitado y está entre 4 y 50 µm, con incerteza de 0,5 µm. La tolerancia típica es de +- 1 % (1,3).
Figura 2: Ilustración del principio de la medición por corrientes parásitas (4).
4- MÉTODO POR FLUORESCENCIA DE RAYOS X
La fluorescencia de rayos X fue introducida en los instrumentos de medición de espesor de capa en el comienzo de los años 80 y la ASTM B 568-98:2009 normaliza esa medición (1,8).
Normalmente es una técnica utilizada para casos específicos, pues la inversión en el equipo es significativa. Cuando los revestimientos son metales nobles aplicados en circuitos impresos e integrados, joyería u otros sectores de la industria electrónica, el alto costo puede ser atenuado en función de las ventajas presentadas. Por ejemplo: áreas con 0,2 mm de diámetro pueden ser medidas con excelente precisión, sin contacto del aparato con la muestra. El espesor de capas sobrepuestas puede ser medido obteniendo resultados individuales. Además del espesor de la capa, es posible obtener la composición. La flexibilidad de esta técnica no destructiva permite la medición en geometría compleja.
Las mediciones por fluorescencia de rayos X se basan en el principio de que la incidencia de un fajo de radiación primaria (rayos X), al interactuar con el material arranca electrones de la capa K de los elementos presentes en el mismo y genera una radiación secundaria fluorescente, característica del material (9).
Un fajo de rayos X (radiación primaria) incide sobre el material y la energía de un fotón de rayos X es absorbida por un electrón de la capa interna K, provocando su arrancamiento. El espacio liberado por el electrón arrancado es ocupado por un electrón de una capa más externa y, al ocurrir este cambio, ocurre la emisión de una radiación secundaria característica del elemento, que es la fluorescencia de rayos X. Esta fluorescencia es detectada en el equipo que la convierte en medidas de espesor. La Figura 3 ilustra el principio que acabamos de describir (9,10).
Figura 3: Ilustración del principio de medición por fluorescencia de rayos X (10).
Un equipo de espectrometría de fluorescencia de rayos X incorpora, básicamente, dos partes: (1) una cámara para acomodar la muestra; (2) un analizador de espectros que procesa la señal de la cámara y la transforma en espesor. La cámara de muestras consiste de un tubo de generación de rayos X y un contador proporcional para detectar los rayos X fluorescidos. El tubo de rayos X es la cabeza del sistema de medidas. Las señales obtenidas en el contador proporcional son amplificadas, transferidos para un discriminador de pulsos y de ahí para el procesador, que acciona un display digital o una impresora.
Las ventajas son la capacidad de medir en partes y áreas pequeñas, la ausencia de contacto con las piezas que serán medidas, la capacidad de medir múltiples capas y la capacidad de medir simultáneamente el espesor y la composición de ligas binarias (1).
5 – CÁLCULOS PARA DETERMINACIÓN DEL ESPESOR DE UN REVESTIMIENTO
Además de las técnicas arriba citadas, que utilizan equipos de medición, está la posibilidad de estimar los espesores de la capa utilizando cálculos basados en las propiedades de los metales del revestimiento y los parámetros del proceso. Las fórmulas para esos cálculos pueden ser obtenidas en el “Manual Técnico de Tratamentos de Superficie (11) de SurTec do Brasil Ltda., que está disponible en la dirección http://www.surtec.com.br/at/surtec_manual_tec_ed2009.pdf
CONCLUSIÓN
Con el avance de las técnicas y equipos de medición de espesores, obtener esa información sobre el revestimiento dependerá, apenas, de la búsqueda por la metodología y equipos que más se adecuan a la realidad de su empresa y de sus productos.
<< Boletin Acabados Superficiales - Edición de marzo 2012
Dra. Célia R. Tomachuk
Doctora en el área de materiales y producción por la Universidade Estadual de Campinas – UNICAMP, habiendo realizado doctorado doble en la Università degli Studi di Napoli “Federico II”, Napoli, Italia. Tiene experiencia en el área de ingeniería de materiales, con énfasis en corrosión, actuando, principalmente, en los siguientes temas: tratamiento de superficie, revestimientos y electroquímica. Actualmente es coordinadora de pesquisa y desenvolvimiento de SurTec do Brasil Ltda.
Dra. Fernanda Martins Queiroz
Maestra y doctora en el área de tecnología nuclear de materiales por el Instituto de Pesquisas Energéticas Nucleares – IPEN/USP, con énfasis en corrosión. Es pesquisadora química del Departamento de Pesquisa e Desenvolvimento de SurTec do Brasil Ltda.
|