PROCESOS DE CINC ALCALINO SIN CIANURO Y PASIVADOR NEGRO TRIVALENTE
"Según el autor, en comparación con otros procesos de cinc, los de cinc alcalino sin cianuro son los que tienen menor costo, pues son necesarios apenas soda cáustica, cinc metal y 20% v/v de aditivos orgánicos."
En última análisis, puede haber razones para que, por proyecto, una capa adicional (normalmente diferente) sea necesaria para garantizar el desempeño deseado de una pieza. Las razones pueden incluir dureza, capacidad de desgaste, lubrificación, brillo u otros requisitos decorativos.
Mientras tanto, lo más común es como un medio para aumentar la resistencia de vida útil o la resistencia a la corrosión de la pieza, actuando como una capa de sacrificio.
Cadmio y cinc protegen el acero galvánicamente o “sacrificialmente”, esto es, en el par de corrosión creado entre el sustrato acero y el metal depositado, el depósito es normalmente anódico y se corroe preferencialmente.
El metal base acero siendo catódico, dentro de la célula de corrosión está protegido, desde que haya cualquier revestimiento en las inmediaciones.
Ventajas de los procesos de cinc alcalino sin cianuro
- Tiene excelente poder de penetración en regiones de baja densidad de corriente;
- Excelente resistencia a la corrosión;
- La micro estructura de los depósitos es granulada menos finamente que los depósitos a base de cloruro y por tanto ideal para la adhesión de la pintura.
- En comparación con otros procesos de cinc, los de cinc alcalino sin cianuro son los que tienen menor costo, pues son necesarios apenas soda cáustica, cinc metal y 20% v/v de aditivos orgánicos.
- Reducción de costos en tratamiento de efluentes, sin generación de residuos, pues el tratamiento consiste en el ajuste de pH y precipitación de óxido de cinc.
Reacciones químicas del proceso
En los baños de cinc alcalino sin cianuro es importante que el cinc se compleje.
El complejo formado en estas soluciones es el “cincato” y es constituido de la siguiente forma:
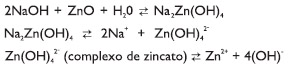
La deposición efectiva es representada como sigue:
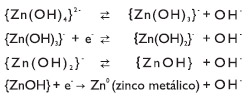
Especificaciones (Zn): Como depósito
Peso atómico: 65,38
Peso específico: 7,14
Peso oz/ft2 por 0,001”: 0,59
Espesor (in) de 1 oz / ft2: 0,00168
Gramo depositado / A-h: 1,219
A-h / ft2 por depósito 0,001”: 14,3
El cinc tiene conductividad eléctrica equivalente a la del latón (26-28% IACS versus 27% IACS del latón).
Esta resistencia equivale a 6,0-6,06 microohm-cm.
Punto de fusión: 419,5ºC
Punto de ebullición (760 mm Hg): 907ºC
Temperatura de combustión: 800ºC (aprox.).
Presión de vapor (419,5ºC): 1,39 X 10-1 mm Hg
Conductividad térmica:
- Sólido (18ºC): 113 W/m.K
- Sólido (410,5ºC): 96 W/m.K
- Líquido (419ºC): 61 W/m.K
- Líquido (750ºC): 57 W/m.K
La mayoría de los procesos de electrodeposición es compuesta de diferentes etapas o fases.
Las piezas a ser bañadas requieren, invariablemente, una limpieza de óleos, grasas y remoción de cualquier óxido metálico, para garantizar buena adhesión de los metales electro depositados sobre su superficie.
Después de la electrodeposición del cinc, es necesaria la aplicación de un pasivador ácido como capa de conversión conteniendo compuestos de cromo, lo que aumenta sensiblemente la resistencia a la corrosión.
Ciclo operacional típico del proceso:
1- Desengrace químico;
2- Desengrase electrolítico;
3- Lavado;
4- Decapado ácido;
5- Lavado;
6- Proceso de electrodeposición;
7- Lavado doble;
8- Activación nítrica 0,5 a 1,0 %
9- Cromatizado;
10- Lavado;
11- “Top Coat” (opcional);
12- Secado.
Limpieza Química y Electrolítica
Toda materia orgánica es removida de la superficie de la pieza para asegurar la buena adhesión del proceso.
Para un desempeño óptimo del proceso de limpieza es conveniente la utilización del desengrase químico y electrolítico como pre tratamiento de las piezas.
Decapado ácido
Cuando la pieza esté libre de materias orgánicas, cualquier óxido metálico, ya existente o formado durante la limpieza electrolítica, deberá ser removido para garantizar la buena adhesión del baño.
Esto es normalmente realizado con el uso de ácidos minerales fuertes (HCl, H2SO4, etc.) diluidos en agua. Estos ácidos disuelven los óxidos de la superficie.
Electrodeposición
La principal reacción que ocurre en los procesos de electrodeposición es la de óxido-reducción. Esto es realzado en baños electrolíticos, donde una corriente es aplicada a través de una solución conductora, o “electrólito”, creando un flujo de electrones entre los dos puntos (“electrólisis”).
Metales previamente disueltos en su estado iónico son entonces “reducidos” para su forma elemental, después de la migración para el cátodo (-).
El diagrama abajo, muestra un esquema típico para baños parados, con la capacidad de aplicación de calor / frio y de “purificación de gases”, aunque en la mayoría de los procesos de galvanoplastia puede no ser necesario.
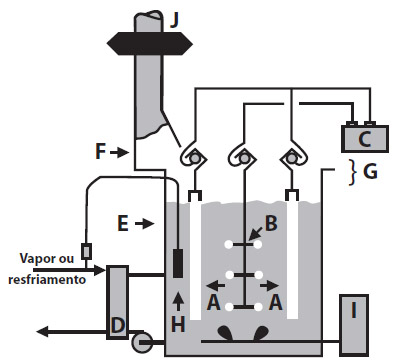
A- Ánodos
B- Piezas
C- Rectificador
D- Calentamiento
E- Tina.
F- Sistema de ventilación.
G- Borde libre.
H- Termopar
I- Filtro / Eductor
J- “Scrubber”
La reacción es de óxido-reducción, en la cual las moléculas de agua son separadas y ambos, oxígeno e Hidrógeno, son liberados en forma de gas en el ánodo (+) y en el cátodo (-), respectivamente.
Entre tanto, el metal depositado sin aditivos especiales adicionados al baño resulta en depósitos groseros y de mala calidad (quema, aspereza, etc.…)
Estos aditivos, que hacen parte de la composición química del baño y auxilian a controlar la fuente principal de conductividad y/o el metal, bien como las propiedades químicas, son generalmente de naturaleza orgánica. Además de regular la velocidad de deposición bajo determinadas densidades de corriente abrillantan e/o refinan la estructura de los granos.
Todas estas propiedades deben ser monitoreadas de cerca y rutineramente, para asegurar una producción libre de problemas.
Principales componentes del baño y sus funciones
Cinc (Zn): Forma el complejo cincato, el cual provee una reserva de metal y regula la descarga de cinc en le cátodo, determinando la eficiencia catódica y el poder de penetración.
Soda Cáustica (NaOH): iones hidroxilos (OH-): este componente regula la conductividad, contribuye para la eficiencia del cátodo y controla la corrosión anódica.
Aditivos
“Carrier” (modificador de eficiencia): Polímeros de cadena larga, iónicos, que migran y envuelven el cátodo, permitiendo un mayor control de la distribución del baño.
Abrillantadores: Materiales catiónicos, proporcionando un profundo depósito brillante.
Purificador / Condicionador: Control de impurezas metálicas, orgánicas y otras.
Condiciones operacionales:
Eficiencia catódica
El efecto de las concentraciones de cinc y de la soda cáustica en el baño sobre la eficiencia del cátodo:
“Troubleshooting”
Los problemas más comunes están dentro de las categorías abajo:
- Contaminación orgánica;
- Contaminación metálica;
- Desequilibrio de los componentes del baño;
- Mala filtración;
- Diversos (mecánicos, etc.)
Pos Baño – “Bright Dip”
Después de alcanzar el espesor deseado, las piezas son lavadas e inmersas en una solución de ácido mineral débil para “pulir” cualquier material orgánico que todavía pueda estar en la superficie.
Esto a veces es llamado de “Bright Dip – inmersión brillante” por su tendencia de abrillantar el depósito.
Solamente después de esto es que la pieza está lista para aceptar una película de conversión de cromato (o revestimiento orgánico) y, subsecuentemente, completar la secuencia del proceso.
Capas de conversión base cromo (Cr+6)
Pros Contras
Fácil de operar Base en Cr+6 (Cromo hexavalente)
Terminación brillante Más caro (Plata como base)
Buena protección contra la corrosión Fácilmente contaminado (Cl)
Restricciones sobre el cromo hexavalente (Cr+6)
RoHS – Directiva 2002/53/EC del EPC – restricción de sustancias peligrosas.
ELV – Directiva 2000/53/EC del EPC – Fin de vida de vehículos.
WEEE – Directiva 2002/96/EC del EPC – Residuos de equipos eléctricos y electrónicos.
JIG – 101 – Declaración de composición de material para productos electrónicos.
OSHA – 29 CFR 1910-1026 – Norma de cromo (VI)
MIOSHA – Part 315 cromo (VI) en industria general.
Introducción de procesos de “HEX-FREE” (Libre de cromo VI)
Reacción del Cr+3 con la disolución del Zn para formar óxidos cinc cromo.
2 CrO43- + 3Zn = 16 H3O ↔ 2 Cr3+ + 24 H2O + 3 Zn2+
Consumo de hidrógeno (H3O) para aumentar el pH.
Formados complejos polinucleares con cromo.
Como ellos son vistos:
Como ellos trabajan:
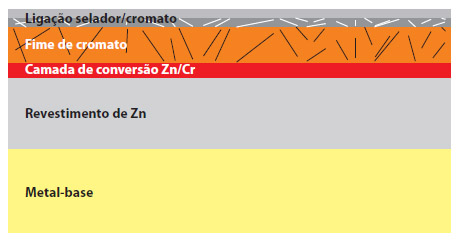
Primeros pasivadores trivalentes negros
Aunque en conformidad con la restricción de las reglamentaciones de sustancias peligrosas, debido al revestimiento de conversión relativamente fino y a la composición química, inicialmente los pasivadores negros trivalentes del mercado tenían graves inconvenientes:
Pros Contras
Libres de cromo hexavalente Más caros
Color menos negro
Poco estables
Menos protección contra la corrosión
Pasivadores negros trivalentes modernos
Más económicos.
Mejor correspondencia de colores con el negro hexavalente tradicional.
Más estable que los productos de los competidores.
Desempeño similar de protección contra la corrosión cuando utilizados con “top coats”
Propiedades Físicas
Espesor 80 a 150 nm (0,08 a ,015 µm)
Negro
Conductividad constante
Soldabilidad
Modelables
Baja resistencia a la abrasión.
Ciclo típico del proceso
Cincado
Lavado doble
Activación con ácido nítrico o sulfúrico
Negro trivalente
Lavado doble
“Top coat” de alto desempeño
Secado
Características necesarias del sustrato
Metal base relativamente plano
Depósitos de grano fino.
Niveles adecuados de abrillantador.
Espesor mínimo de 7,6 µm
Factores de control
TTC/P donde:
T= Tiempo de inmersión → 20 a 40 s
T= Temperatura →24 a 30 ºC
C= Concentración →2,0% A & 4,0 a 8,0% B
P=pH → 1,8 a 2,2
Efectos del tiempo de inmersión
Inmersión corta Inmersión larga
Depósito manchado Decapado acelerado
Depósito marrón Iridiscencia
Iridiscencia Agotamiento de la solución
Efectos de la temperatura
Temperatura baja Temperatura alta
Depósito fino Desplaque acelerado
Desplaque del baño Iridiscencia
Depósito opaco Depósito opaco
Efectos de la concentración
Concentración baja Concentración alta
Iridiscencia Desplaque del baño
Desplaque acelerado Depósito marrón
Depósito fino Depósito polvoriento
Efectos del pH
pH bajo pH alto
Tiempo de reacción más rápido Tiempo de reacción más lento
Desplaque del depósito Capa de conversión más espesa
Aunque haya inicialmente cuatro variables que controlan la terminación negra (TTC/P), la terminación negra trivalente dependerá del baño de cinc subyacente.
Cuando el baño de cinc es satisfactorio y los otros parámetros fueron atendidos (incluyendo mínima contaminación, etc.) la terminación negro brillante debe ser libre de iridiscencia (la capa mínima de cinc sugerida es de 5,08 µm).
Características de la película de conversión
Barrera mecánica.
Resistencia a la abrasión relativamente baja.
Color
Resistencia a la corrosión.
Conductividad constante.
Características de la resistividad eléctrica sobre el cinc.
Tipo de cromato µΩ/in2
Ninguno 20 – 50
Incoloro – azul 50 – 100
Amarillo claro 100 – 250
Amarillo oscuro 250 – 500
Verde oliva 800 – 1000
Negro trivalente (Sin top coat) 50 – 100
“Top coats” & sellantes
Silicatos para protección contra la corrosión.
Modificador de torque para los límites superior e inferior, da profundidad, brillo y protección.
Cr libre silicatados y/o poliméricos, con dispersión del negro, dan brillo y profundidad de color.
Pasivador libre de Cr6+ para protección superior y aumento de brillo.
Polímeros para brillo uniforme.
Métodos de análisis
Método analítico.
Titulación con solución de tiosulfato de sodio 0,1N
Espectroscopia de absorción atómica (AA)
Ensayos físicos.
Niebla salina (ASTM B-117)
Humedad 100%@100ºF (ASTM D-2247)
Resistencia a la abrasión.
Resistencia a la niebla salina
Film Cromato - Horas niebla salina
Incoloro – hexavalente 8-24 horas
Incoloro – trivalente 8-24 horas
Amarillo iridiscente - 72-20 horas
Amarillo bronce - 96-44 horas
Verde oliva 144-216 horas
Negro (base plata) 24-120 horas
Negro trivalente con “top coat” 48-120 horas
Equipos
Tinas – Acero inoxidable, Koroseal revestido, polietileno, polipropileno.
Cestos – Acero inoxidable revestidos en plastisol, polipropileno.
Gancheras – Revestidas en plastisol.
Resistencias – Acero inoxidable , cuarzo, Teflón.
Agitación – por inducción a aire.
Mark Siegrist
Gestor Técnico Sénior de Cuentas de la Haviland Products company.
|